Warehousing and distribution operations have undergone significant changes over the years. With the continued focus on faster and more efficient supply chains, warehouses are becoming the epicenter of key strategic and operational decisions. However, the industry still faces various challenges that threaten to stunt growth and undermine operational efficiency. In this blog post by PLM Companies, a nationwide logistics and supply chain company, we have highlighted some of the key industry issues facing warehousing operations today.
Industry Issues Involving Warehousing
Industry Issues Involving Warehousing
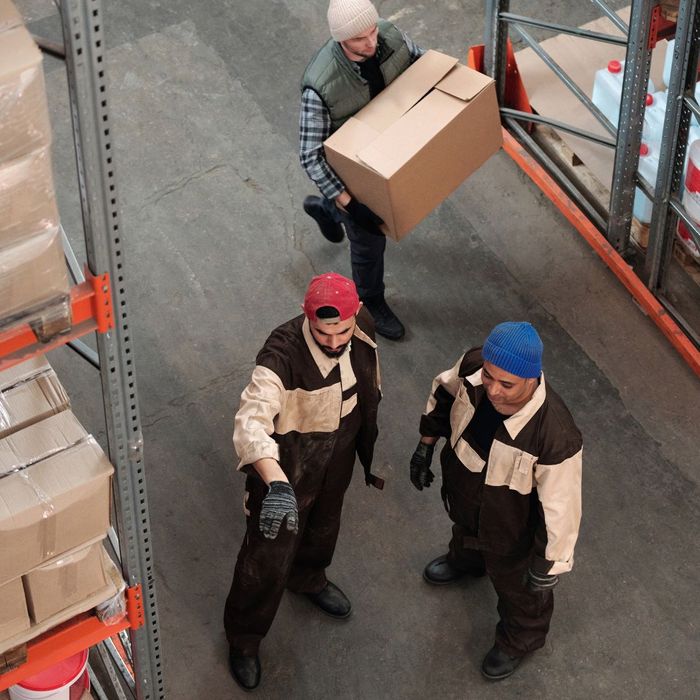
1. Shortage of Skilled Labor
The warehouse industry is facing a significant shortage of skilled labor, which can be attributed to various factors such as demographics, changing workforce preferences, and a lack of career growth opportunities. In many cases, warehouse jobs are perceived as low-paying with limited career prospects, leading to a widening skills gap in the industry. This shortage has created a vacuum that is hampering operational efficiency and driving up labor costs.
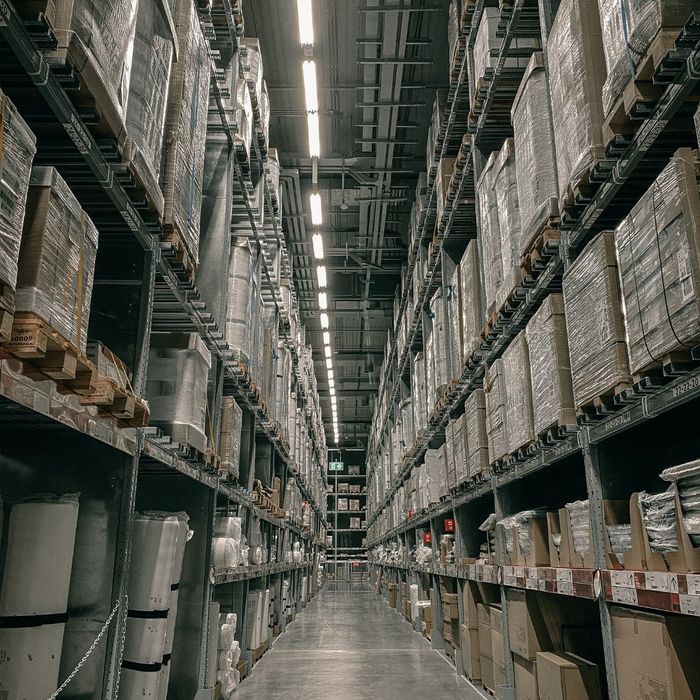
2. Managing Supply Chain Disruptions
The recent global supply chain disruptions caused by the COVID-19 pandemic have exposed the vulnerabilities and complexities of warehousing operations. Disruptions in the supply chain can lead to shipping delays, inventory shortages, and other operational bottlenecks that can impact the bottom line.
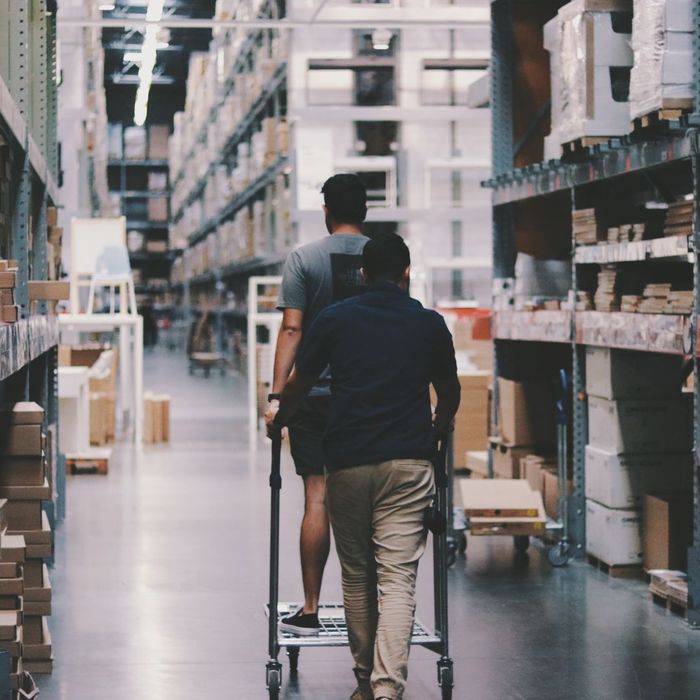
3. Lack of Space
Warehouses are facing a shortage of space, as e-commerce and omnichannel fulfillment needs increase. Many warehouses are struggling to keep up with demand due to the limited space availability. The lack of space leads to issues such as the inability to expand product offerings or meet customer demand.
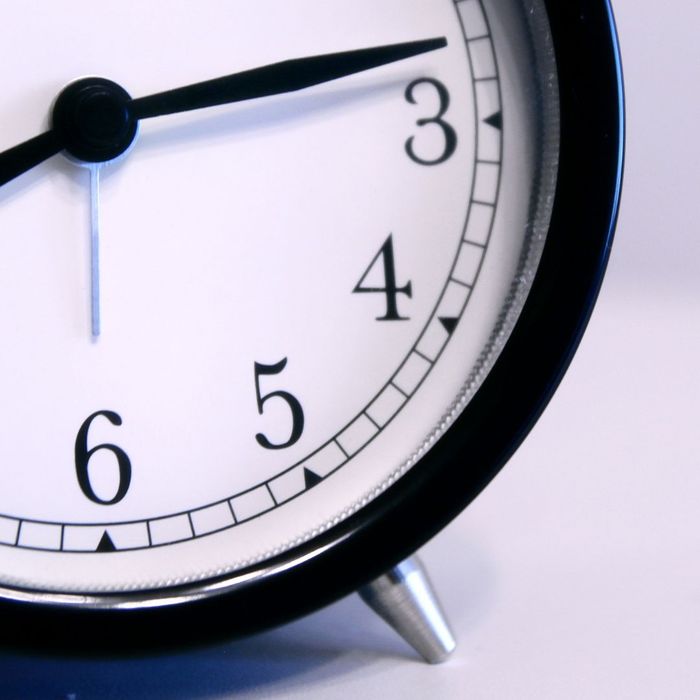
4. Time Constraints for Packaging and Pallets
A common industry issue facing warehousing operations is that packaging and pallets are often relegated to lower-priority tasks. Warehousing teams often have to prioritize tasks such as unloading and processing new inventory, picking and packing orders, and shipping products, leaving little time to handle packaging and pallets. This often leads to delayed shipments, increased costs, and decreased operational efficiency.
By partnering with PLM Companies, businesses in the Midwest can benefit from our industry expertise, tailored solutions, and commitment to delivering efficient and sustainable outcomes for your supply chain needs. Contact our team to learn more!